What is Porosity in Welding: Typical Sources and Effective Solutions
The Science Behind Porosity: A Comprehensive Overview for Welders and Fabricators
Understanding the complex devices behind porosity in welding is essential for welders and fabricators making every effort for impressive workmanship. From the make-up of the base products to the complexities of the welding process itself, a wide variety of variables conspire to either exacerbate or minimize the visibility of porosity.
Comprehending Porosity in Welding
FIRST SENTENCE:
Exam of porosity in welding discloses crucial insights right into the honesty and high quality of the weld joint. Porosity, identified by the visibility of tooth cavities or spaces within the weld metal, is an usual worry in welding processes. These spaces, otherwise properly addressed, can compromise the structural honesty and mechanical buildings of the weld, bring about possible failings in the ended up item.
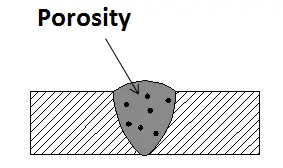
To find and measure porosity, non-destructive testing methods such as ultrasonic screening or X-ray examination are usually utilized. These techniques allow for the identification of inner flaws without jeopardizing the integrity of the weld. By assessing the dimension, form, and circulation of porosity within a weld, welders can make educated decisions to boost their welding procedures and attain sounder weld joints.

Aspects Affecting Porosity Development
The occurrence of porosity in welding is influenced by a myriad of factors, ranging from gas shielding efficiency to the ins and outs of welding specification setups. One essential element contributing to porosity formation is inadequate gas shielding. When the securing gas, commonly argon or carbon dioxide, is not successfully covering the weld swimming pool, climatic gases like oxygen and nitrogen can pollute the molten steel, resulting in porosity. Furthermore, the cleanliness of the base materials plays a significant function. Pollutants such as corrosion, oil, or moisture can vaporize throughout welding, producing gas pockets within the weld. Welding parameters, consisting of voltage, present, take a trip rate, and electrode type, likewise impact porosity development. Utilizing incorrect settings can generate too much spatter or warm input, which subsequently can result in porosity. The welding Get More Info technique used, such as gas metal arc welding (GMAW) or secured metal arc welding (SMAW), can influence porosity development due to variations in warmth circulation and gas coverage. Understanding and regulating these elements are crucial for reducing porosity in welding procedures.
Impacts of Porosity on Weld High Quality
The existence of porosity also deteriorates the weld's resistance to corrosion, as the entraped air or gases within the spaces can react with the surrounding atmosphere, leading to degradation over time. In addition, porosity can impede the weld's ability to hold up against pressure or influence, further threatening the total high quality and reliability of the bonded framework. In vital applications such as aerospace, automotive, or architectural buildings, where safety and web link longevity are critical, the destructive impacts of porosity on weld quality can have serious effects, highlighting the relevance of decreasing porosity through correct welding methods and treatments.
Methods to Reduce Porosity
Furthermore, making use of the ideal welding specifications, such as the appropriate voltage, current, and travel rate, is critical in preventing porosity. Preserving a constant arc size and click this angle throughout welding additionally aids minimize the probability of porosity.

Utilizing the suitable welding technique, such as back-stepping or using a weaving activity, can likewise aid distribute warmth evenly and reduce the opportunities of porosity formation. By implementing these methods, welders can effectively minimize porosity and create top quality welded joints.
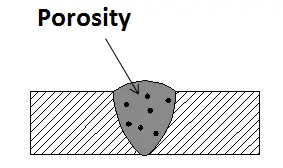
Advanced Solutions for Porosity Control
Applying sophisticated innovations and ingenious techniques plays a critical role in achieving remarkable control over porosity in welding procedures. Additionally, utilizing advanced welding strategies such as pulsed MIG welding or modified ambience welding can also help reduce porosity problems.
One more advanced remedy involves using advanced welding devices. Utilizing devices with integrated functions like waveform control and innovative power resources can boost weld top quality and reduce porosity risks. The implementation of automated welding systems with exact control over criteria can significantly reduce porosity defects.
Furthermore, incorporating innovative tracking and examination innovations such as real-time X-ray imaging or automated ultrasonic testing can help in detecting porosity early in the welding process, enabling instant corrective activities. Generally, incorporating these sophisticated remedies can substantially enhance porosity control and improve the overall quality of welded elements.
Verdict
In conclusion, recognizing the scientific research behind porosity in welding is crucial for welders and makers to create top notch welds - What is Porosity. Advanced services for porosity control can better improve the welding process and ensure a solid and reliable weld.